Keywords: self-alighting roller bearings, Spherical roller bearing, bearing ring, bearing ring processing
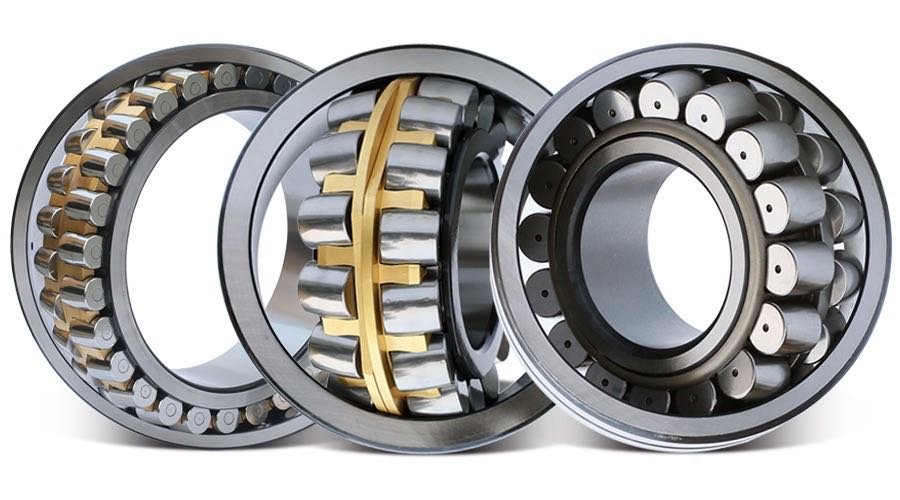
There are three common structures of self-alighting roller bearings, two of which are shown in the figure below. The inner ring 02 has a small retaining edge, distributed on both ends, and each has a roller gap, 180 degrees apart. The gap is convenient to load the appropriate roller 04. Retainers 46 or 66 of this type are generally made of brass. After assembling the finished product, it is necessary to check the turning flexibility of the bearing, but after turning the outer ring 01, it is found that the roller falls off from the cage, or the roller is pulled out with a little force at the gap, and the roller will disengage from the bearing along the gap.
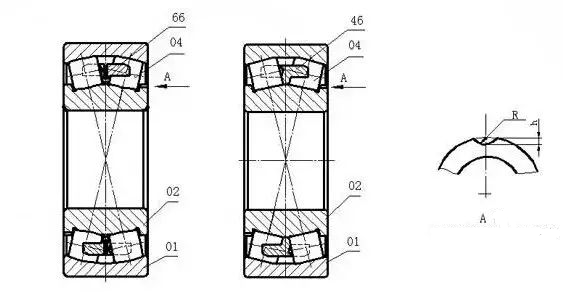
Cause analysis of roller falling off
The general assembly process of self-aligning roller bearings is as follows: The outer diameter of cage 46 or 66 sets of inner ring 02 is loaded with appropriate roller 04 from the roller gap on the small rim of the inner ring to form the inner ring assembly, but one or two cage pocket holes are symmetrically left in each row, and rollers are not installed at first. Put the inner component into outer ring 01 and fill the same group of rollers from the gap in the cage pocket hole. And in the inspection of flexible rotation, some rollers fall off from the cage, or in the gap with a little hand force, rollers from the gap, so it needs to be analyzed from the bearing related parts one by one, the analysis is summarized as follows:
Influence of bearing ring processing
①The influence of bearing inner ring small rim car processing
Bearing inner ring car processing small flange outer diameter according to the requirements of the product drawings for “-” tolerance, usually -0.35 ~ -0.15mm, and the depth size of the design gap is generally only the basic size, no tolerance. The actual machining is controlled within the range of ±0.2mm according to the accuracy tolerance of the current machine tool, and the measurement of the notch depth is based on the outer diameter of the small rim (see Figure 2 below). The depth of the oil groove size tolerance according to the current processing industry standard press control + / – 0.15 mm, so the depth (small guard outside diameter to the distance to the center of the oil groove) shallow small guard, usually depth size no more than 3 mm, could produce tolerance accumulation effects in practical processing (guard outside diameter, depth of the gap size for a minimum size, oil groove depth for the largest size). Finally resulting in roller end face and retaining the minimum contact area, sometimes contact parts even close to the oil groove. Therefore, in the gap, a little force will roll out along the gap. However, for the deep edge, due to its large contact area with the edge, a relatively small tolerance impact, sometimes even can be ignored.
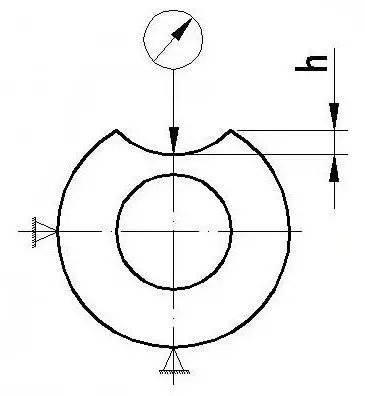
②Influence of grinding of the small rim of bearing inner ring
The small rim of bearing inner ring grinding is grinded by the fixed distance method. Due to the reasons of turning to process, the machining allowance of small guard edge grinding is small or the uneven grinding of grinding plane process, resulting in black skin after grinding. Usually, the black skin can be removed normally so that the thickness of the small rim is small. For the shallow small rim, the contact area of the end face of the roller itself is small, and the axial distance of the roller along the inner ring increases after the grinding of the small rim so that the roller is easy to come out along the gap, as shown in Figure 3 below.
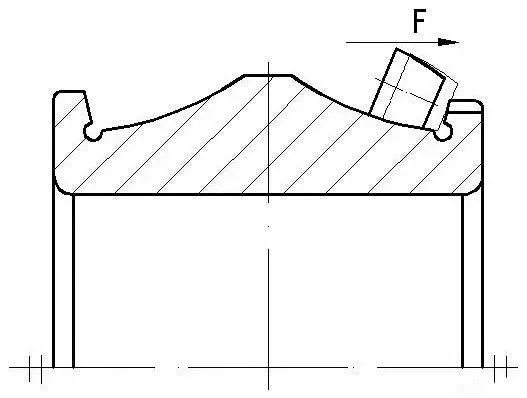
③Influence of grinding process on the raceway of bearing ring
Bearing outer ring grinding process raceway grinding, sometimes found a few grinding still black skin. Due to machining and heat treatment, the grinding allowance is small or the outer raceway is deformed, resulting in black skin after grinding. Usually, the outer raceway is ground, and the black skin can be moved down normally when it is ground off. In this way, the inner raceway is underground to realize the normal assembly process. In this way, the central diameter of the roller group is overall outside, so that the contact part of the roller and the rim is outside, and the actual contact area is small after the gap is outside, so that the roller is easier to come out along the gap.
The influence of cage processing
Cage machining is usually carried out by drilling holes on a drilling machine through the positioning of a bisector die. Due to the manufacturing without special machine tool processing, mold manufacturing precision is low, and sometimes even face process maintains a base surface flatness are super bad, cause pocket machining depth dimension is not unified, generally by adjusting the repositioning drilling machine tool, the result is a deep hole, round hole diameter is larger, and after loading roller, roller and cage clearance is big, And along the cage axial channel-momentum, finally filled with rollers, rollers and cage overall gap is large. In testing the bearing slewing it is easy for the roller to fall off from the cage. In addition, to measure the center diameter of the cage, by measuring the distance control of the measuring column, the caliper force is different, and the skew degree of the pillar is also different (the position of the pillar in the pocket hole). Therefore, the final measurement size can only be used as a reference, and cannot effectively reflect the real measured value of the center diameter. For medium – and large-sized bearings, the effect of this measurement method is small because of its deep retaining edge. For small bearings, because of its shallow guard edge, the influence is greater, sometimes the actual center diameter is large, and the measurement is qualified, such a situation often occurs. After the center diameter is large, the overall center of the roller group is outside, leading to the contact part of the roller and the small guard edge is outside, and the actual contact area is small after the gap is outside, finally causing the roller to escape from the gap.