Bearing cage, also known as bearing retainer, is one of the main parts of bearings. Its function is to encase and isolate the rolling body and move with it, and it usually has the function of guiding the rolling body.
The main function of the cage
- Keep a proper distance between the rolling bodies to prevent the rolling bodies from contacting each other to reduce friction;
- Make the rolling body evenly distributed, so as to make the load evenly distributed;
- Guide the rolling body in the no-load area to improve the rolling conditions in the bearing and prevent damaging sliding.
The cages are subjected to stresses caused by friction, strain and inertia forces, as well as to chemical corrosion of lubricants, additives in lubricants or substances produced by their aging, organic solvents or coolants. Therefore, the design and material of the cage are very important for its performance and the reliability of the bearing.
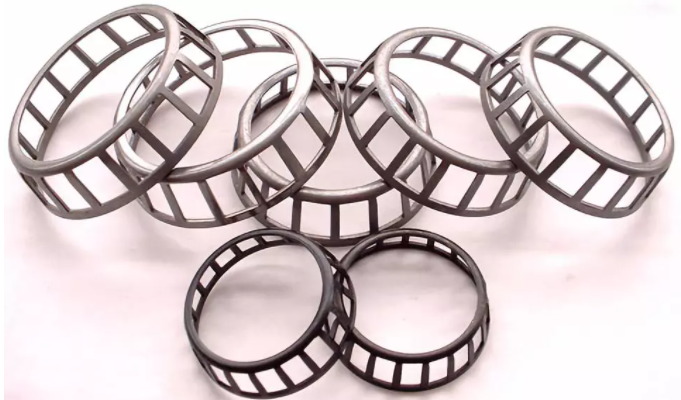
Type of cages
Bearing cages are divided into stamping cages (figure 1), solid cages (figure 2) and prop cages.
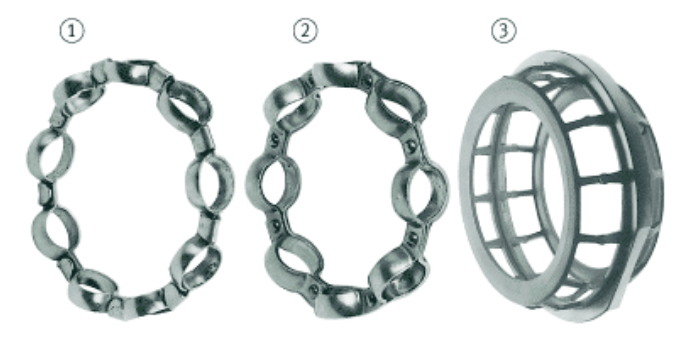
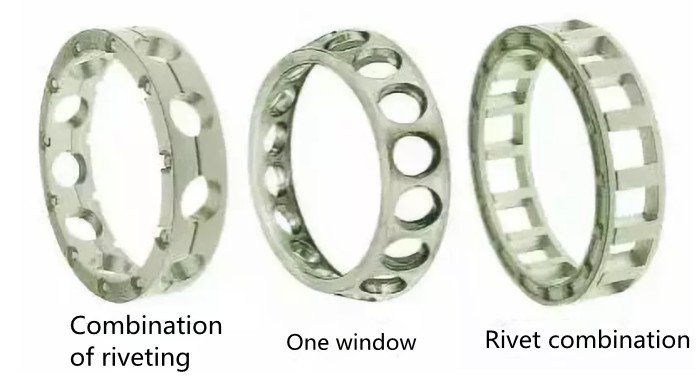
- The advantages of the stamping cage are lightweight, large space inside, which is convenient for lubricant to enter;
- The solid cage can usually allow a higher speed. When the bearing has other forms of motion other than rotation, especially at high speed, the machine cutting metal cage should also be used;
- The pillar cage is threaded through the perforated roller with pins, and both ends of the pins are fixed on the washer. This cage is light in weight and can accommodate more rollers. It is only used for extra-large roller bearings.
Material of bearing cages
The cage materials mainly include stamping steel, machine cut steel, stamping brass, machine cut brass, polymer materials, etc
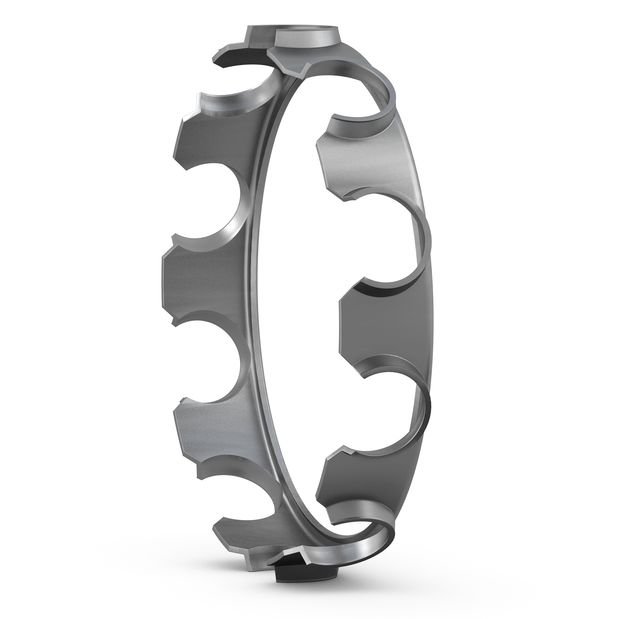
Material: Made of 08 and 10 high quality carbon steel sheet by cold stamping.
Advantages: lightweight, good toughness, easy to process, occupy the small gap between the inner and outer rings of the bearing, lubricating oil is easy to enter the bearing and stay in the cage.
Application: Stamped steel cages are generally used for medium and small bearings.
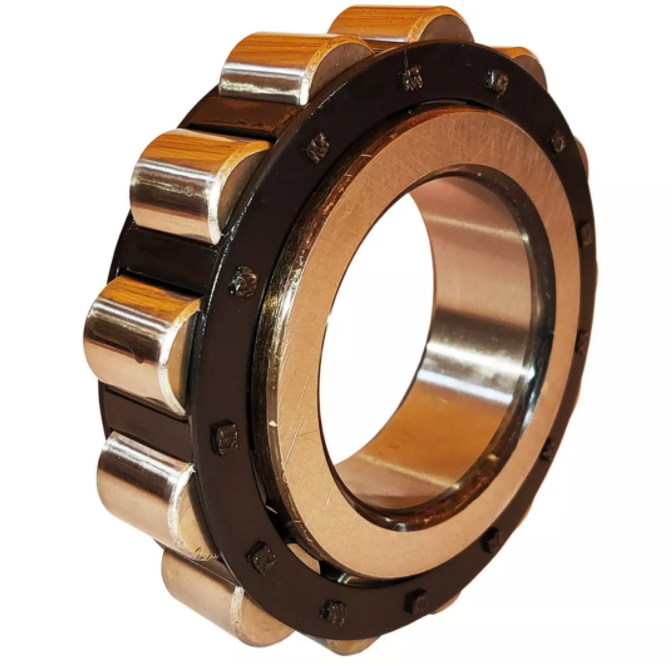
Material: refined from carbon steel forgings.
Advantages: heavier, high strength, good rigidity, low price.
Application: medium and large bearings generally adopt solid cages

Material: refined from high strength brass castings.
Advantages: high strength, good vibration resistance, small friction coefficient, good thermal conductivity, more expensive price.
Application: medium, large and extra-large bearings; Requirement of high speed, vibration, strong impact of the working environment.
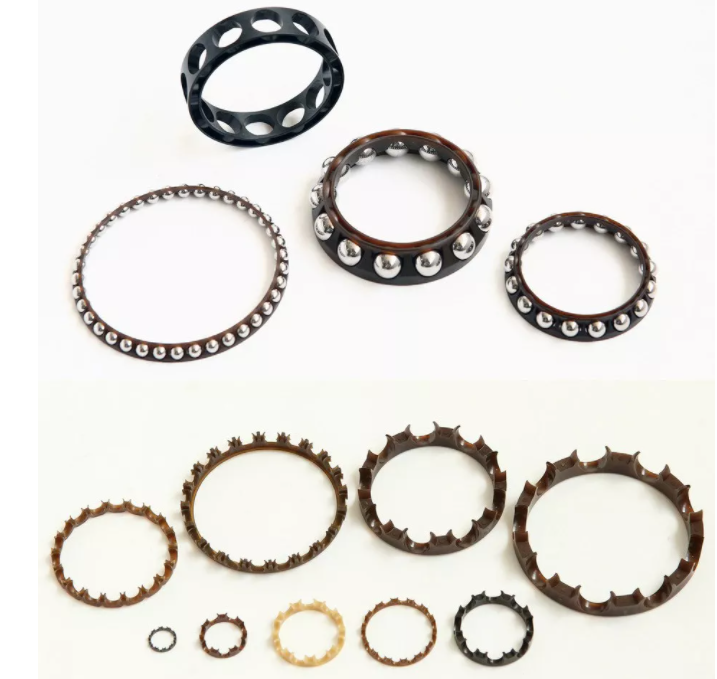
Materials: mainly polymer and its composite materials, including nylon, phenolic tape, polytetrafluoroethylene, etc. Advantages: lightweight, low friction, good strength and elasticity, good shock resistance and lubrication performance. Application: medium, small and miniature bearings; Where high speed is required.
In addition to the above kinds of the cage, other materials such as stainless steel, aluminum alloy, zinc alloy can be used according to special circumstances. In addition, different types of cages are often used for the same type of bearings according to the working conditions in order to achieve the maximum use benefit. Such as:


Causes and measures of cage failure

Common cage failure phenomenon:
· Cage damage
· Loose or broken rivets
· The cage is broken and the rolling body is scattered
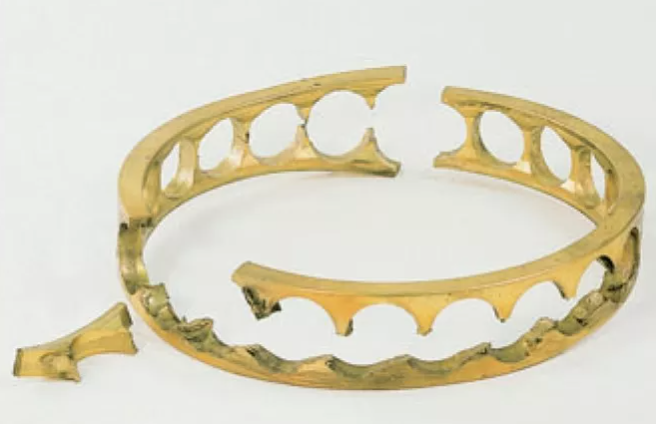
Cage failure reasons:
· Excessive torque load
Large, vibration
· High speed or frequent change of speed
· Poor lubrication
· Foreign body gets stuck
· Poor installation (centerline incline)
Improvement measures:
· Check lubrication conditions
· Check usage conditions
· Improve the installation method
· Select the appropriate type again according to the usage conditions